Setting Up Shop in the U.S.
Debunking Auto Tariff Myths
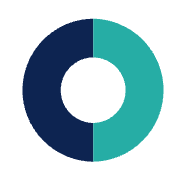
Business Data Lab
Canada and Mexico are the American auto parts industry’s largest and most critical trading partners, accounting for 58% of U.S. auto parts imports and 76% of U.S. exports.
While it is theoretically possible for the U.S. to reshore manufacturing, shifting auto and auto parts sourcing away from Canada to avoid the 25% tariff, it would take a long time, cost a lot of money, and introduce new risks to the supply chain.
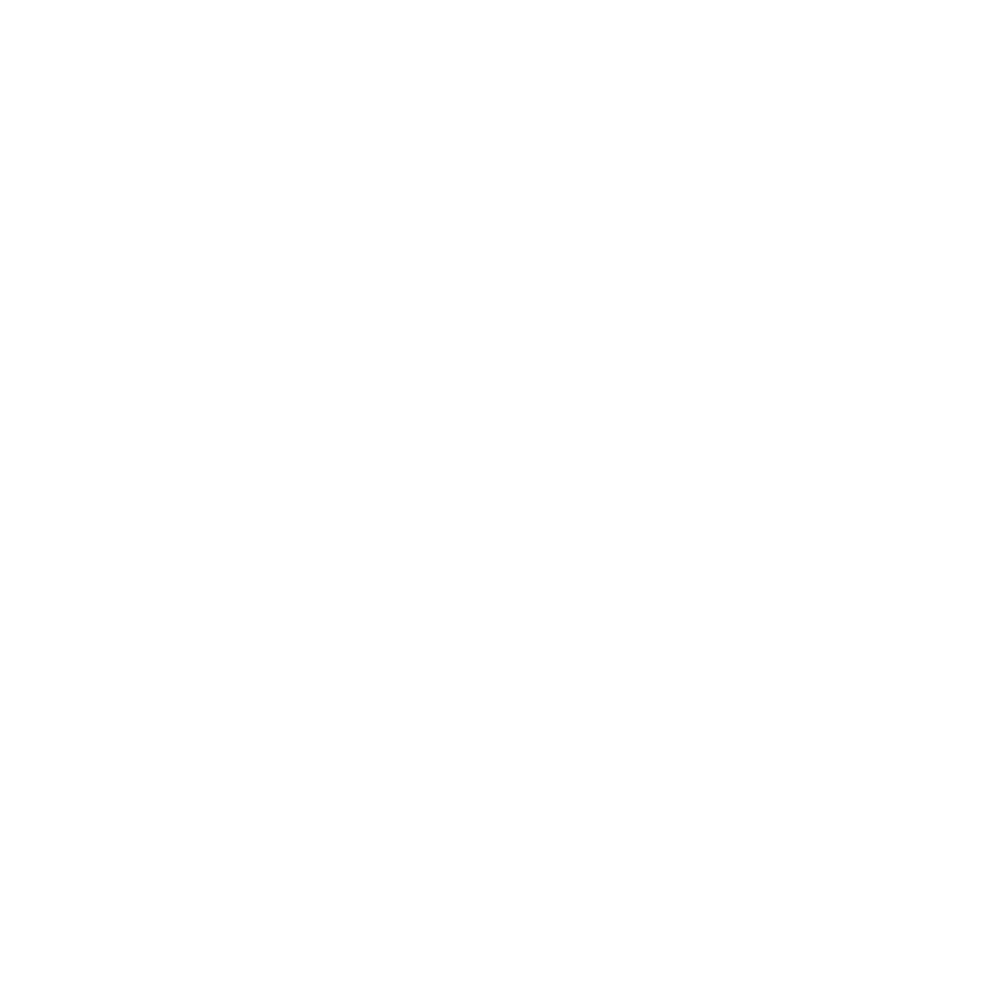
Myth: “We can just make these parts in the U.S.”
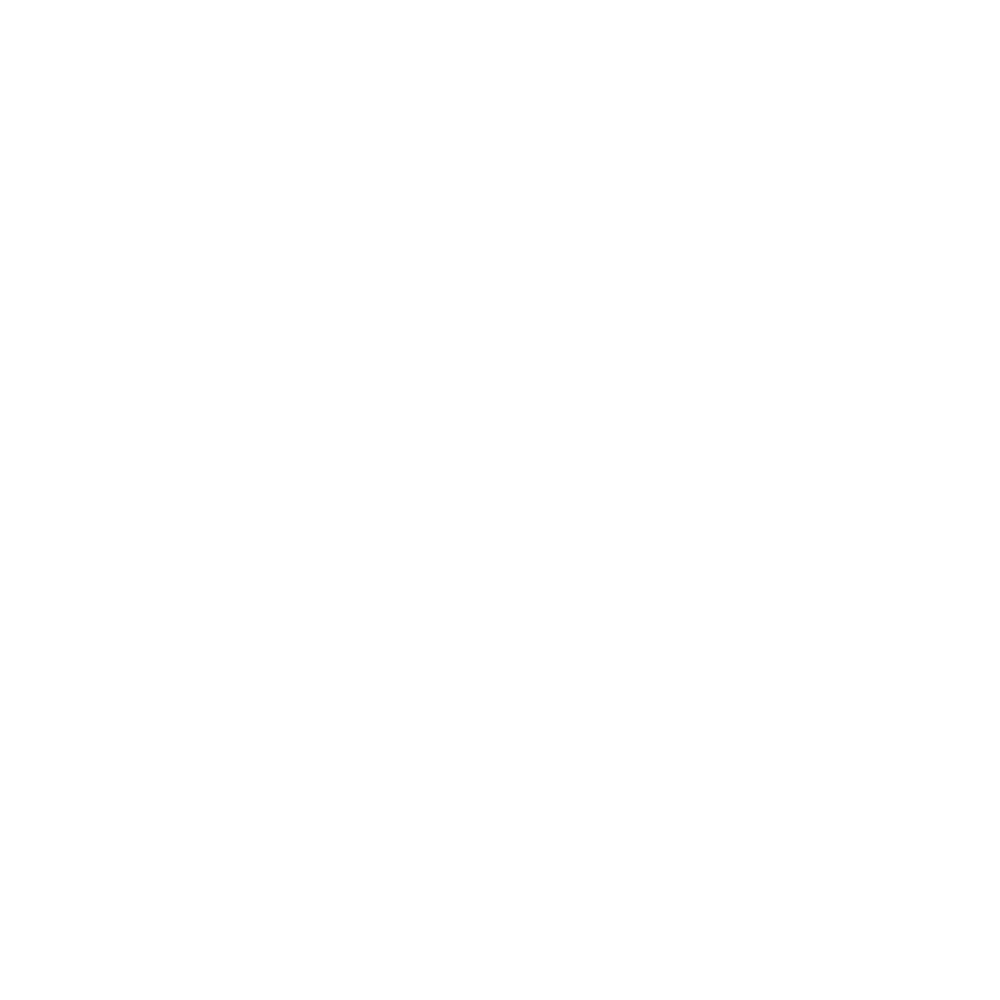
Reality:
- The U.S. already operates at ~70% capacity for vehicle parts, leaving little slack to capitalize on.
- Shifting production would require an average capital investment of $2.3 billion per facility and 1.5–3 years to build (from planning to completion).
- Labour costs in the U.S. are 31% higher than in Canada.
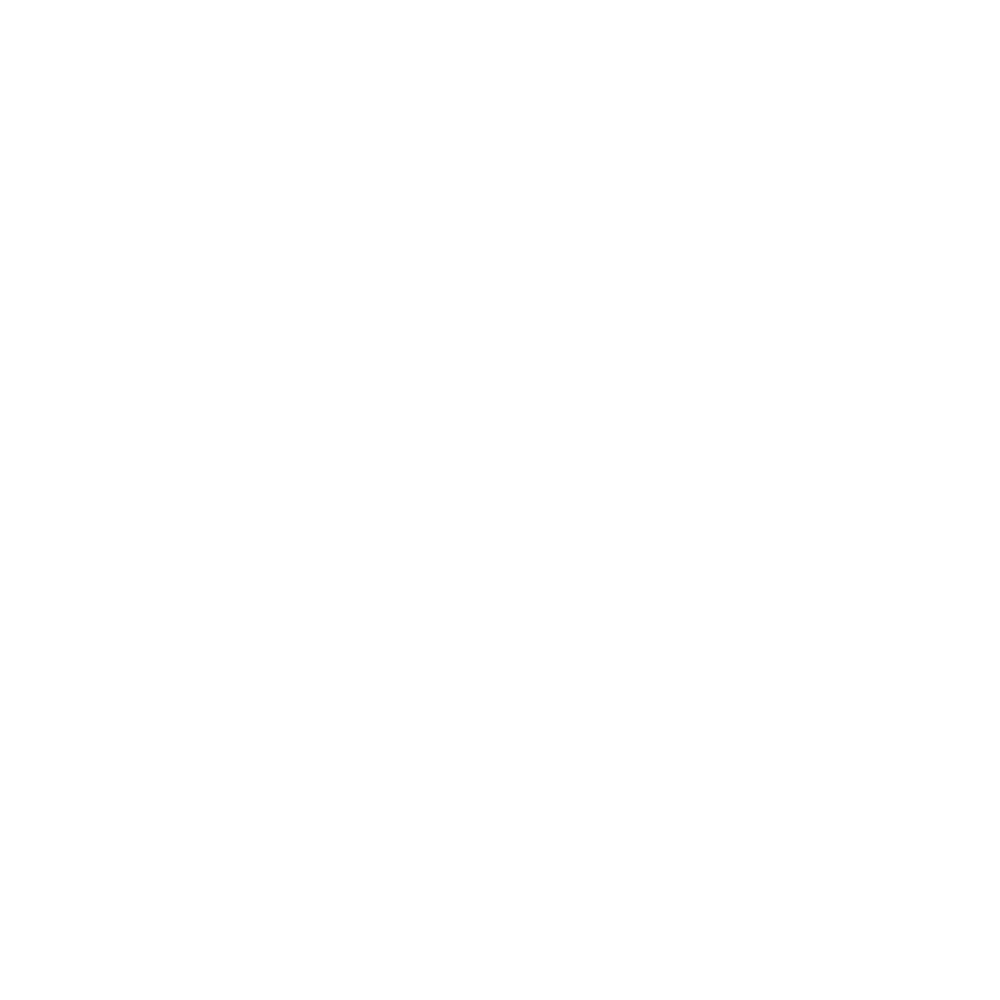
Myth: “We can just switch to other foreign suppliers.”
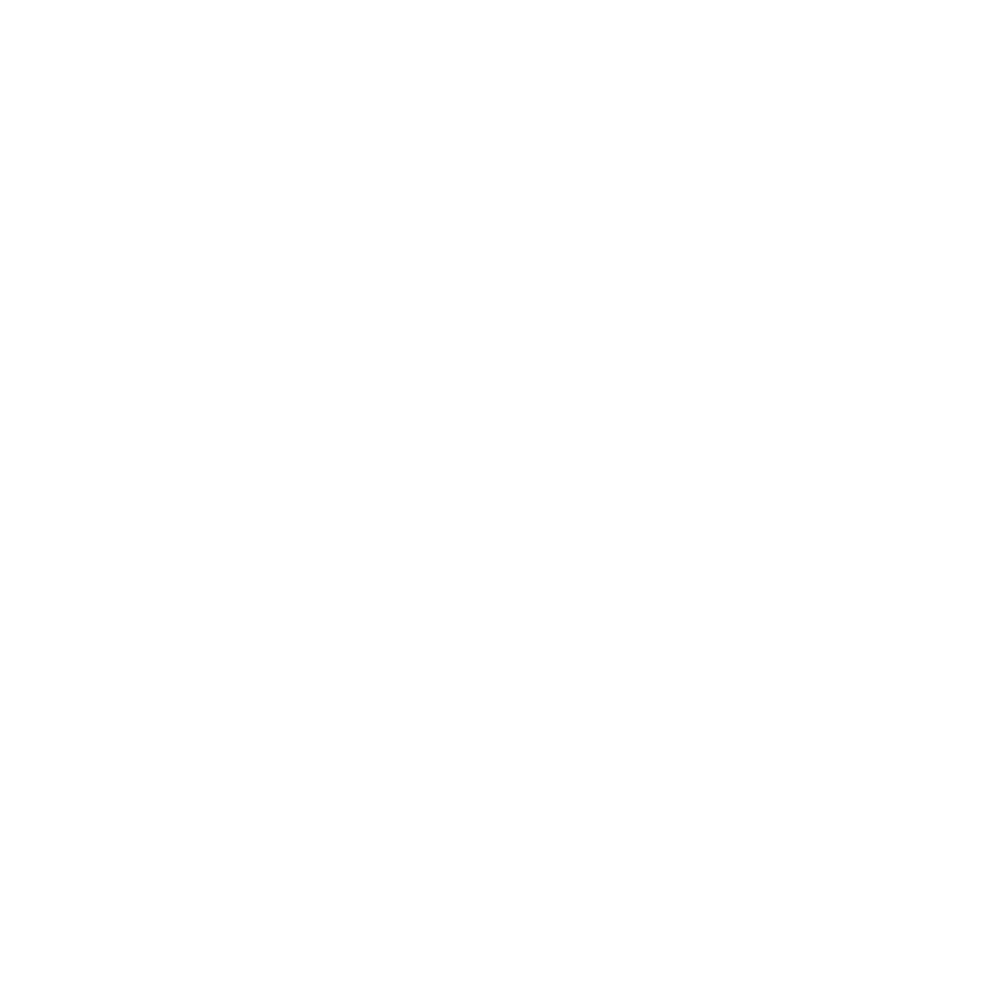
Reality:
- Other potential suppliers like Germany, Japan, South Korea, Austria, Hungary and Poland typically support European or Japanese original equipment manufacturers, not U.S. producers.
- U.S. producers would face longer lead times, higher logistics costs, regulatory mismatches, and geopolitical uncertainty that poses a long-term risk to consistent supply.
- China is a risky option due to national security concerns as well as political volatility.

Myth: “Canadian suppliers can just move to the U.S.”
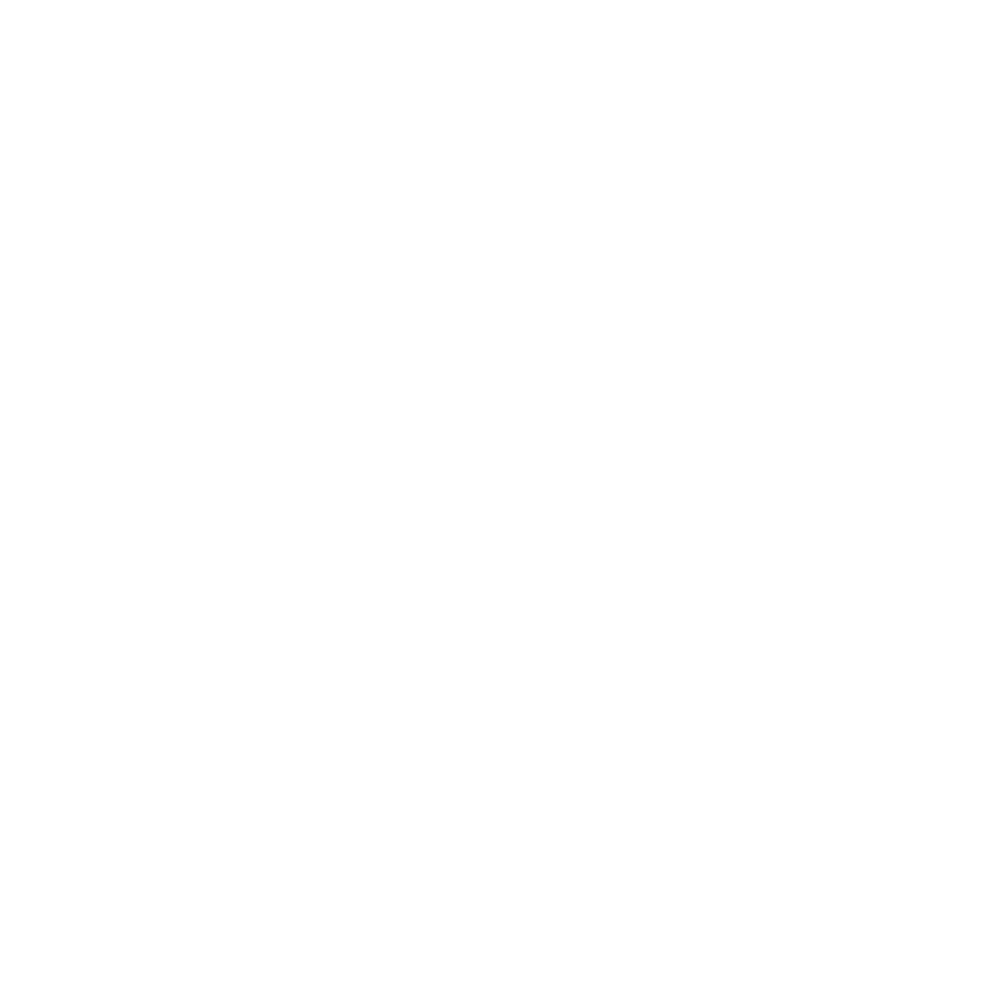
Reality:
- If Canadian auto parts suppliers were to relocate to the U.S. to avoid the tariffs, they would face:
- $50–200 million in closure costs per facility.
- Higher U.S. labour (31%) and regulatory costs.
- Multi-year delays to get U.S. operations up and running.
- Given the temporary and political nature of tariffs, most firms would rather absorb costs than relocate.
Replacing Canadian-Assembled Vehicles
While much of the focus is on replacing Canadian auto parts, full vehicle assembly presents an equal or greater challenge. Canada exports approximately 1.5 million fully assembled vehicles annually to the U.S., accounting for 8‒10% of domestic U.S. consumption. At least six new assembly plants would need to built in the U.S. to cover what they normally buy from Canada.
The Cost of Auto Tariffs on Consumers
- Building new facilities or expanding existing ones in the U.S. would raise the overall price of a vehicle anywhere between $3,500 to $9,000, adding to existing affordability challenges.
- Cancelling existing contracts with Canadian suppliers would result in breakage fees of up to $500 million per facility, with the costs likely being passed in part or in full to U.S. customers.
- Canada supplies 12% of total U.S. auto parts imports, many of which are critical to maintenance and repair. With a 25% tariff applied, that equals roughly $4 billion in additional annual costs passed along the supply chain. If even half of that gets passed to consumers via repair and maintenance, that’s around $2 billion in total increased spending.
- The increase in car prices due to tariffs results in higher repair costs, which subsequently raises insurance premiums. Tariffs on steel and aluminum could further increase repairable claims costs by 1% to 2%. As repair parts become more expensive and cars cost more to fix, these expenses will likely be passed on to consumers, resulting in higher premiums when policies are renewed.
There is a reason that Canada and the U.S. produce cars together — it makes sense economically, which makes sense financially for car owners.
Sources
Analysis by the Canadian Chamber of Commerce’s Business Data Lab (BDL), based on trade data, industry benchmarks, and sector-level impact estimates to assess the potential effects of U.S. auto tariffs on supply chains, consumer costs, and cross-border production.
- State of American Auto Manufacturing Report (2024)
- American Automobile Labeling Act Report (2025)
- Trump Tariffs on Mexico, Canada, China, BRICS Imports Could Strain Over $100 Billion Automotive Parts Industry (2024)
- American Automakers, Investing for the Future (2022)
- Setting the Record Straight on Canada-U.S. Trade (2025)
- Unifor’s Pattern Agreement
- U.S. Bureau of Labour Statistics
- Capacity Utilization: Manufacturing: Durable Goods
- Who Are Ford’s Main Suppliers? (2021)
- Stellantis Plant Fact Sheets
- The tariff ripple effect: how insurers can navigate inflation and market disruptions (2025)
- The “Perfect Storm” of Rising Auto Insurance Premiums and Repair Costs: A Detailed Overview (2024)
- Tariffs Will Make Car Insurance Even More Expensive (2025)
Other Blogs
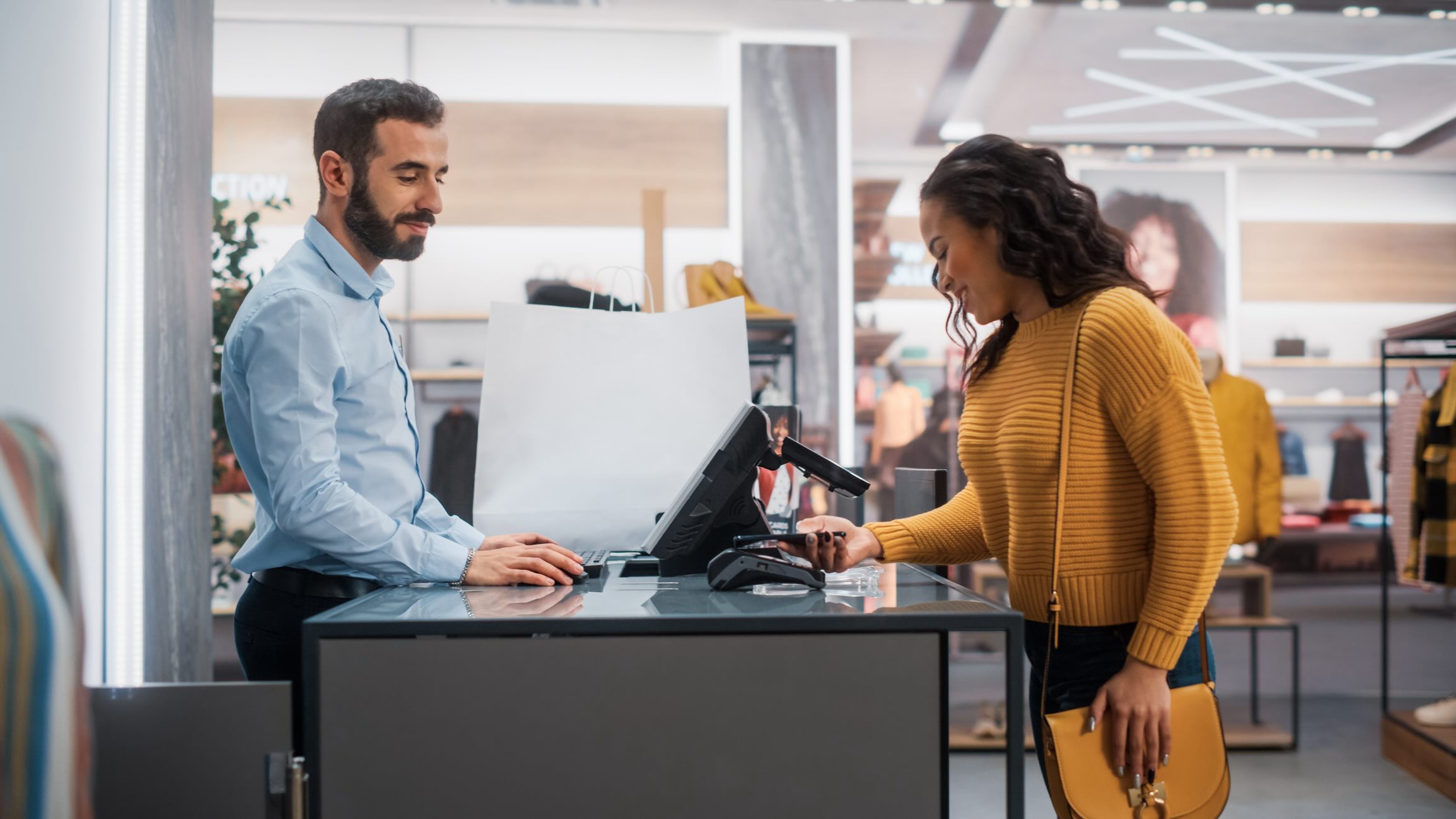
Aug 22, 2025
Retail Sales June 2025: Broad-based rebound as core sales strengthen
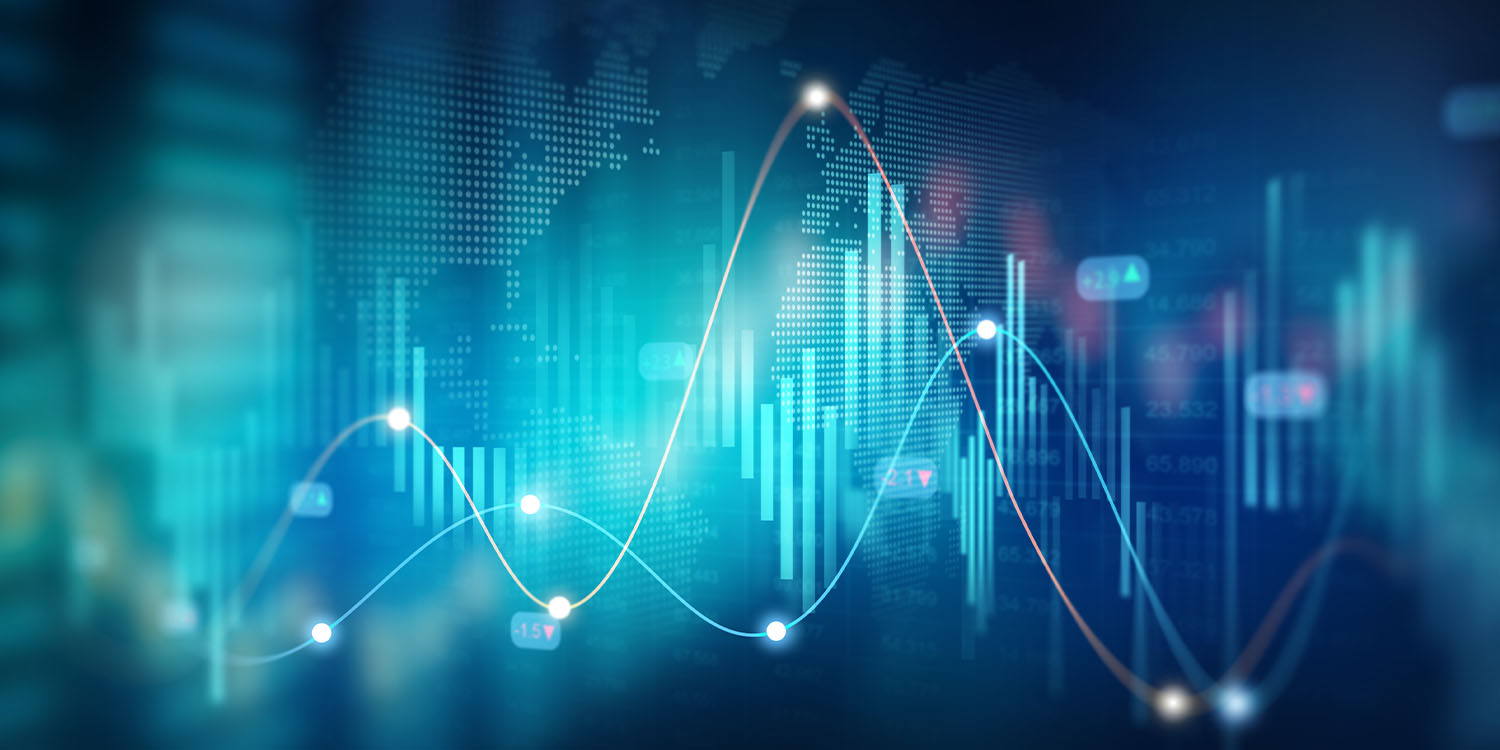
Aug 19, 2025
July 2025 CPI: Inflation cools off in the summer heat.
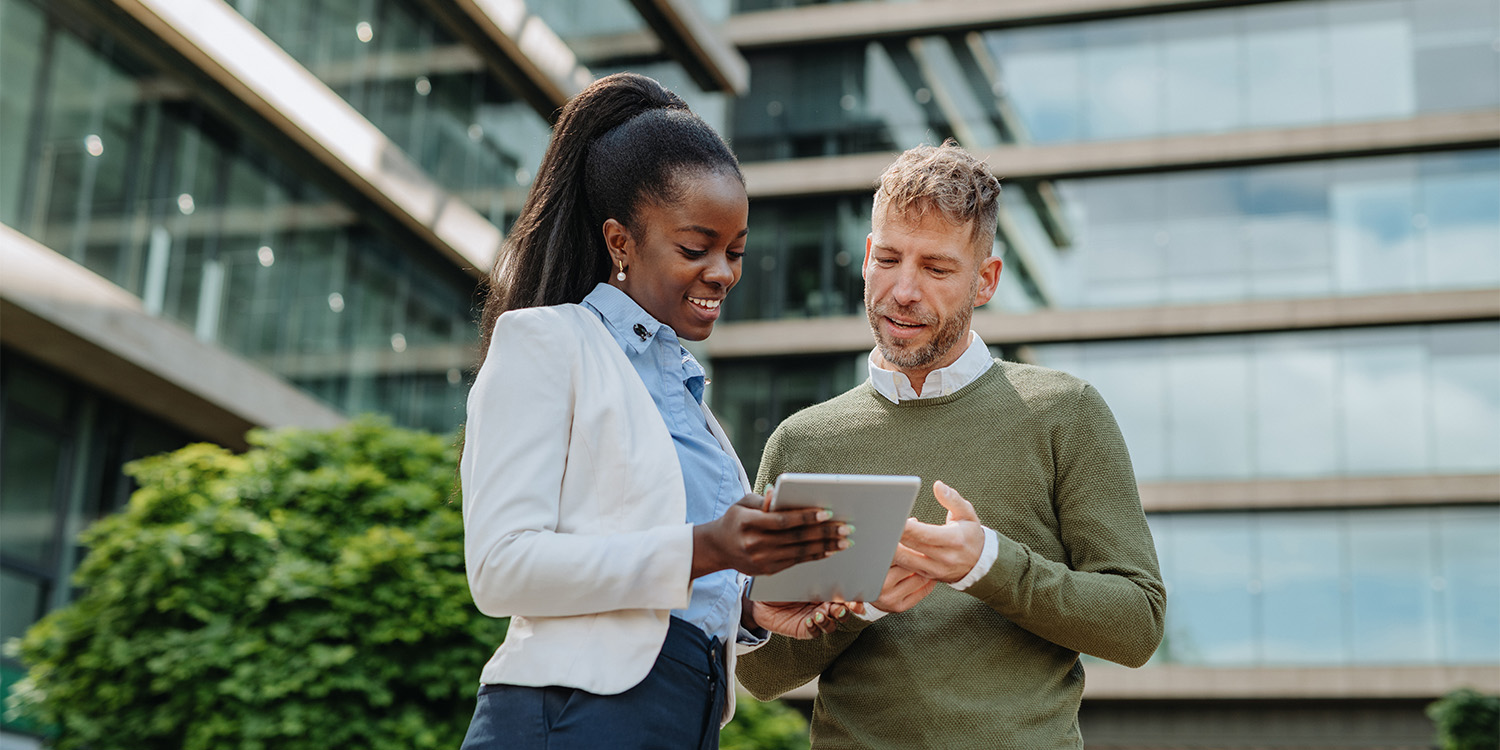
Aug 08, 2025